Voyageur Express
UPDATE: December 16th
Voyageur Express NOW OPEN!
Thank you to everyone who made a turnout for the Grand Opening!
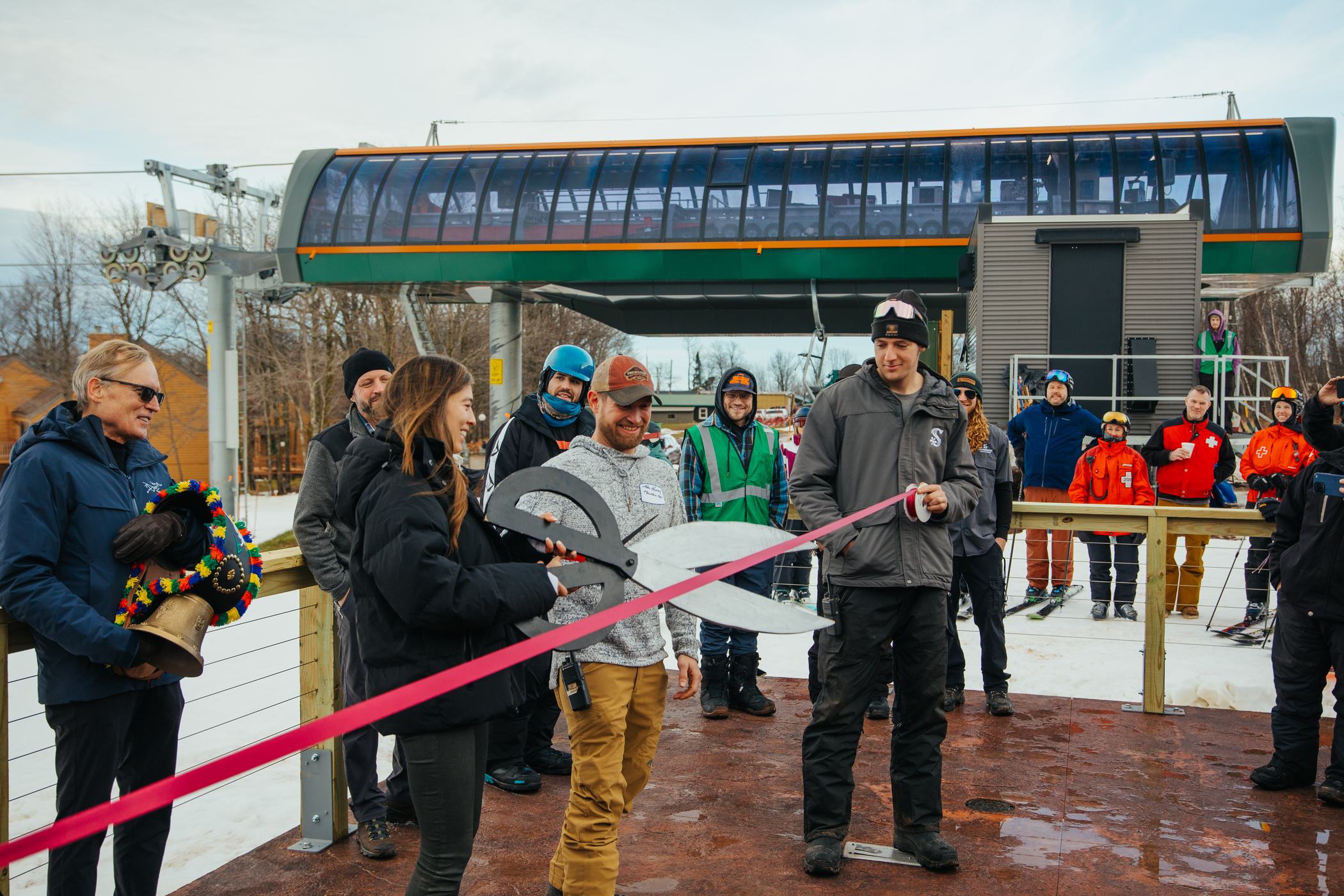
UPDATE: November 23rd
This was a big week for our Lift Project team. On Monday the 20th, after a weekend full of unloaded tests, the Doppelmayr engineers signaled it was time to load up the lift for its acceptance test. The acceptance test, often referred to as the "load test" or "dynamic test" is a procedure by which each chair on the lift is loaded with 110% of the designed weight capacity and put through its paces. Water is the easiest, heavy thing to move around, so that's the common medium for performing these tests.
Our team loaded up 6 cardboard boxes onto each chair and filled them up to a calculated level to ensure an accurate load was put onto each chair. Once all the chairs on the uphill side of the lift were filled, the engineers began their tests. Those include the obvious, making sure the electric motor and evacuation drives will move the lift under the heavy load, but their series of tests are also designed to test all of the redundant systems to ensure they each function on their own. For example, the lift has 4 different brakes, all of which are tested independently to ensure they can stop the lift and hold the load without needing assistance from any of the others. While these brakes would typically work together under normal operating conditions, seeing them each do the job on their own sure is reassuring.
After a full day of testing, the lift successfully passed all of them, marking the official completion of our biggest project of the summer!
UPDATE: November 8th
While the warmer weather hasn't been ideal for snowmaking, it has allowed us to stay focused on the completion of the Voyageur Express. Over the past few weeks, the team has been buttoning up the terminals, making the electrical connections, and aligning the sheave wheels. This week's focus has been on pulling the communication lines down from the top terminal, across each of the towers, and down into the return station at the bottom. A mix of standard copper wiring and fiber optics (think spinal cord) are used to transmit signals to the lift's computer (brain), to allow it to monitor and respond to a host of different safety switches, sensors, and operator controls. This is the first step of the final stage of electrical work before the lift is ready to spin.
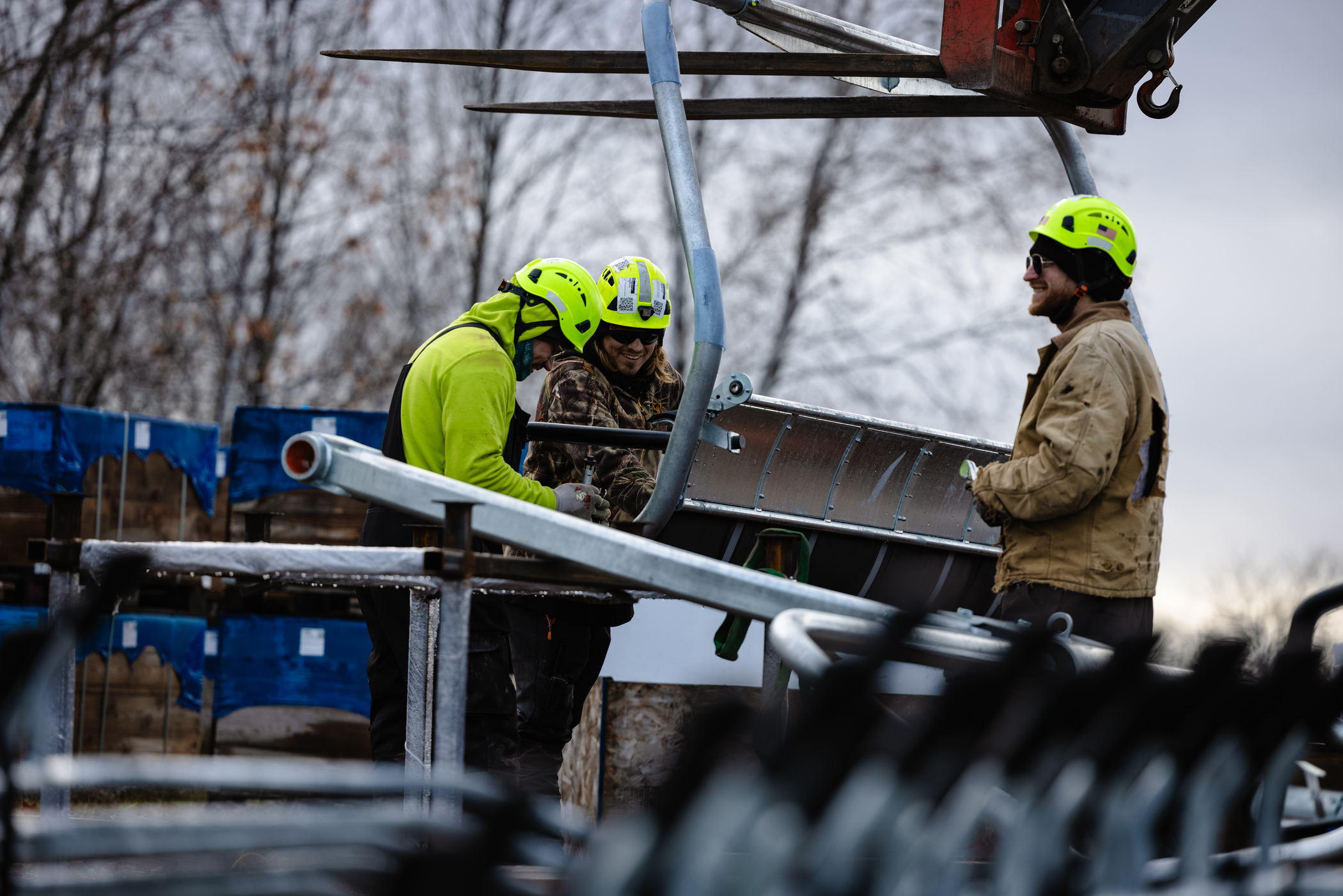
As the electricians from Ruotsala and Doppelmayr work together on the lift's communications, the Snowriver team has been busy assembling each of the 53 chairs for the lift. Arriving in August from Taiwan neatly nested and packed for shipment, there is some assembly required. Each chair gets outfitted with a cushy seat cushion, armrests, and a hanger attached. The back pad, restraint bar, and grip will be added as they're installed onto the lift. By the end of this week, we should be just about ready to do that.
UPDATE: October 17th
After a summer filled with concrete pouring and steel erection, the time has come to string the cable for the new Voyageur Express. With the spool of new 44mm cable (wire rope in ski industry lingo) in place at the return terminal, the crew started by stringing out a much smaller cable, called the lead line. Starting from the top terminal, the team pulled the small cable down each side of the lift line by hand, climbing each tower and hoisting it up and over the sheave wheels before continuing on down the line.
Once the lead line was pulled down both sides, the uphill side was spliced into the haul rope, and the downhill side was attached to a large winch. Once connected, the winch was used to pull the new haul rope all the way around the lift, leaving two overlapping sections between towers #2 & #3. Next the two ends of the haul rope will be spliced together, creating the full loop that will carry the chairs. With that step complete, the lift is looking very close to complete. It won't be long now!
Update: September 29
With the return terminal substantially completed, the lift-build crew set their sights on the drive terminal. We welcomed Keweenaw Crane Company back for another week of heavy lifting. The drive terminal included some of the heaviest picks of the project, including the drive platform. This assembly of carriage, bull wheel, electric motor, and gearbox was the largest at 32,000lbs.
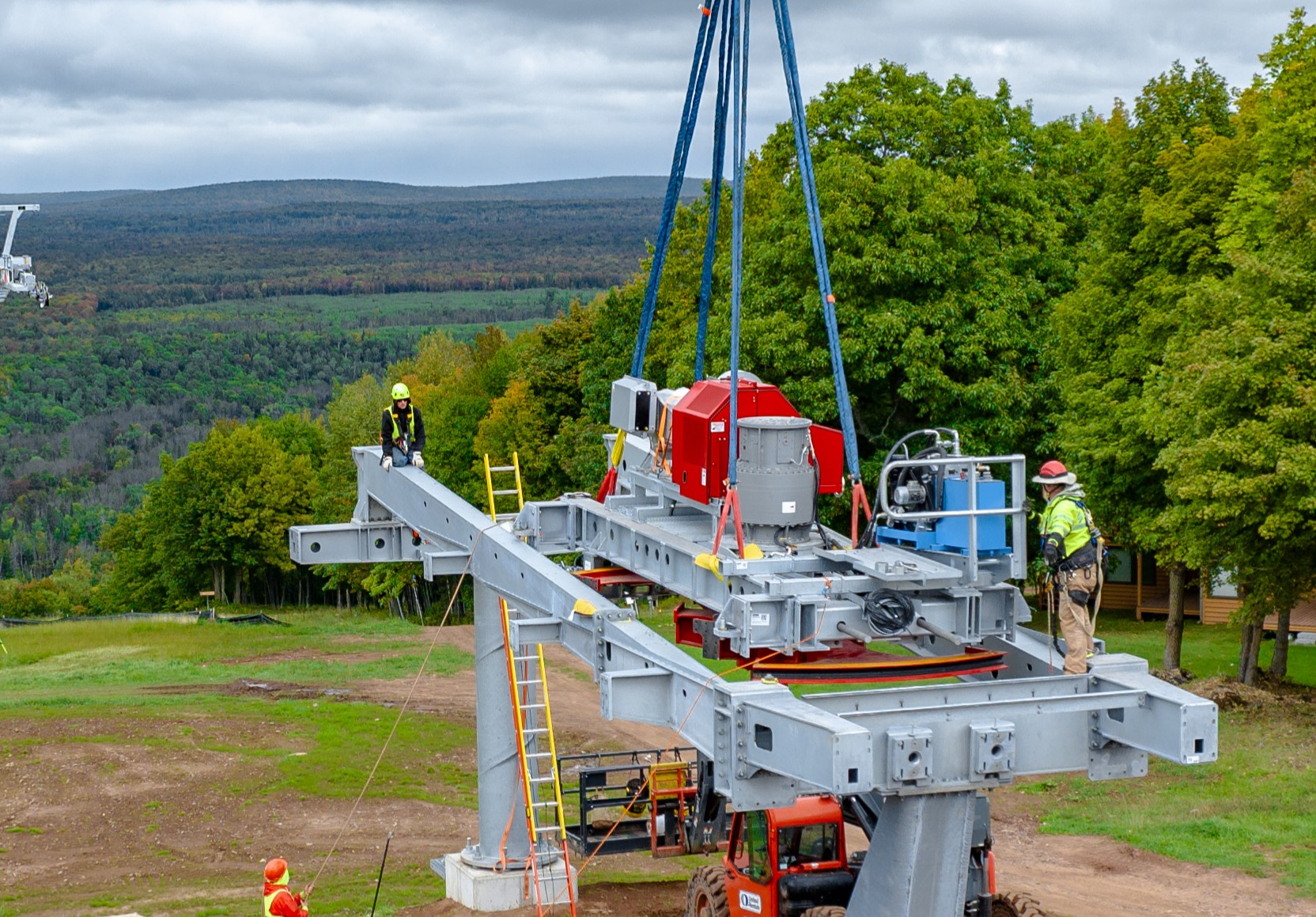
Once installed onto its tracks, the rest of the terminal structure was constructed around it, piece by piece over four long days. The final tower was installed on the last day with the crane on-site, completing all major structures of the lift. From there, the team began assembly and installation of the windows, floor panels, and cladding which is expected to wrap up by October 2nd. Electricians from Doppelmayr are scheduled to arrive then to begin the complex task of bringing the lift to life, a process we expect to take the full month of October.
UPDATE: September 14
After taking a week to stage and prep the components for installation, our partners from Keweenaw Crane Service were scheduled to begin work on Tuesday, August 22nd. The crane was brought over from Calumet on Monday afternoon and set in place to be ready for an early morning start the following day. Each terminal takes approximately four 10+ hour days of crane time to assemble. Each piece is lifted into position, where our crew meticulously bolts them together while the crane holds steady waiting for everything to be tightened up. It's a heavy equipment ballet as more and more pieces are brought from the staging area by forklift and then lifted into place by the 150-ton crane. After months of site preparation and pouring concrete, it's incredible just how fast the terminal comes together. In the week after the crane work is finished, the team meticulously torques every bolt to spec and works to install the finishing touches like windows and siding to enclose the terminal. After the majority of the work was completed at the base of the hill, attention turned to the summit where all of the drive station components needed to be pre-assembled in anticipation of the crane's return on September 12th.
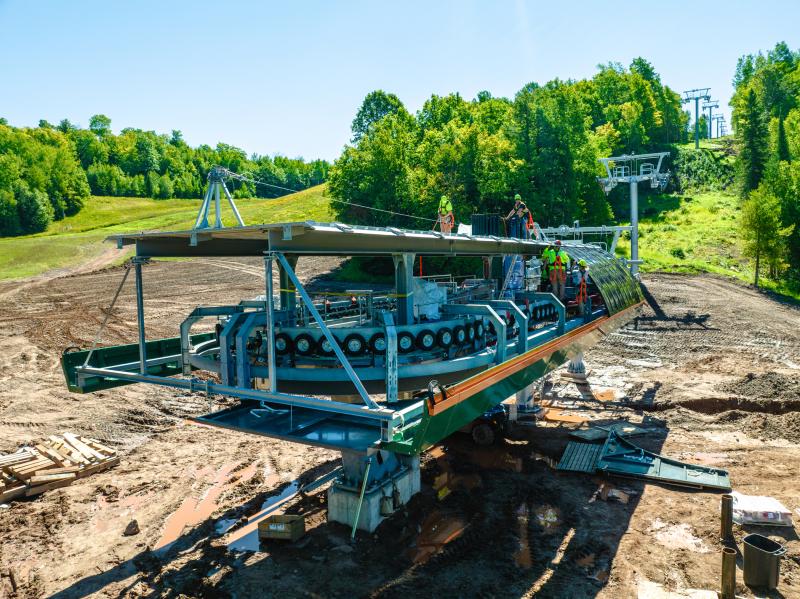
UPDATE: August 8th
Work on the new chairlift is ongoing. Over the past few weeks since the towers were installed, our team has been working their way down the mountain torquing all of the bolts to spec, one by one. That work should wrap up by the end of this week. With the towers now in place, our ground crew has been focused on re-vegetating all of the terrain that was disturbed during construction along the lift line. The sooner we can get vegetation growing on the steep sections of the disturbed slope, the better. The team has been attentive to building diversion ditches, spreading seed, laying straw mat, and setting up silt fencing in strategic locations to prevent the rain from causing erosion. It's great to see the new growth popping through already after only a week's time to germinate.
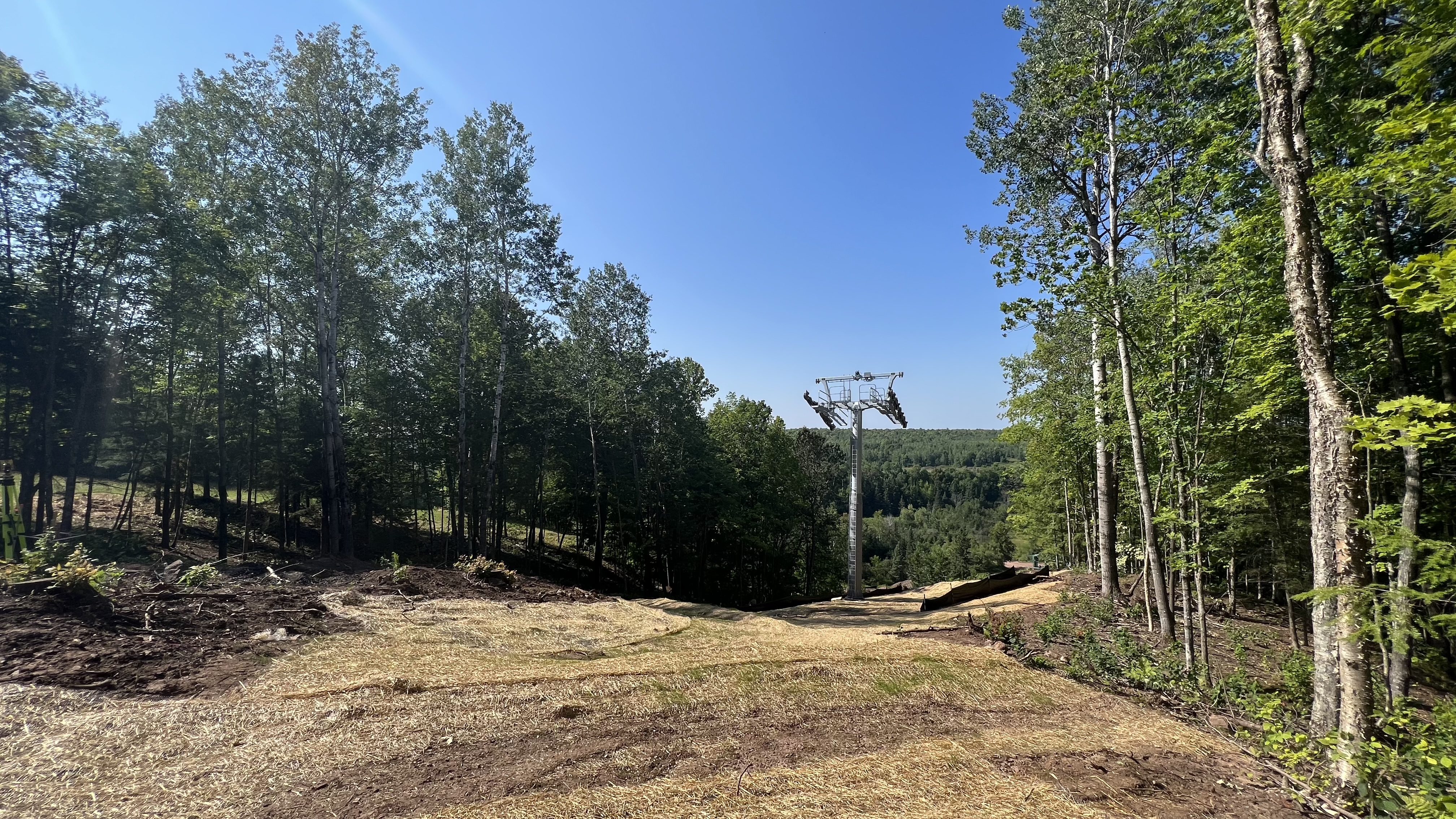
Backfilling at the drive terminal site is now complete. Since the new lift is unloading at a higher elevation than the surrounding terrain, the new foundations weren't placed very deep into the ground and extra material beyond what was excavated was needed to completely cover them. In the photo below, you can see their excavator removing material from the former unloading site of the Quad Chairlift and placing it into a large off-road dump truck for the short trip to the top of the new lift. The big equipment quickly ate away at the mound and in no time it was completely gone.
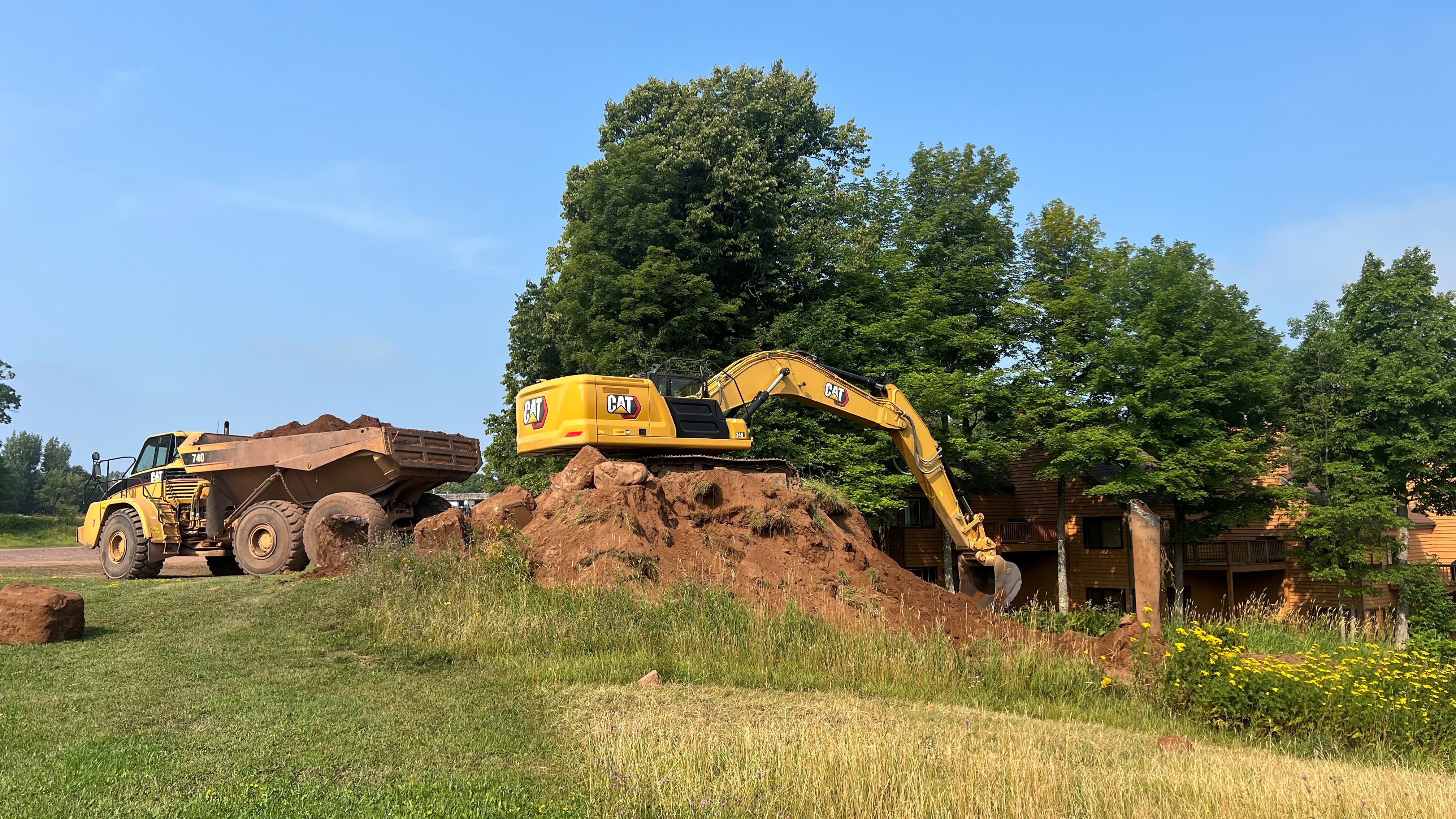
With all the dirt now in place at the top of the VX6, it is really starting to look like a lift could actually land there. For the last month or so it was looking like we were building one heck of a tree stand up at the top of the mountain. As of yesterday, we received our first shipment of terminal steel from Salt Lake City with the remaining components scheduled to ship out of Canada by the end of the week. Terminal assembly is on track to begin towards the end of the month. Erik and the crew have been hard at work staging materials and preparing for the terminal builds to ensure a smooth and quick assembly once the crane is on-site. Stay tuned to our live cams and watch as the terminals go vertical. Soon, this thing is going to start looking like the real deal!
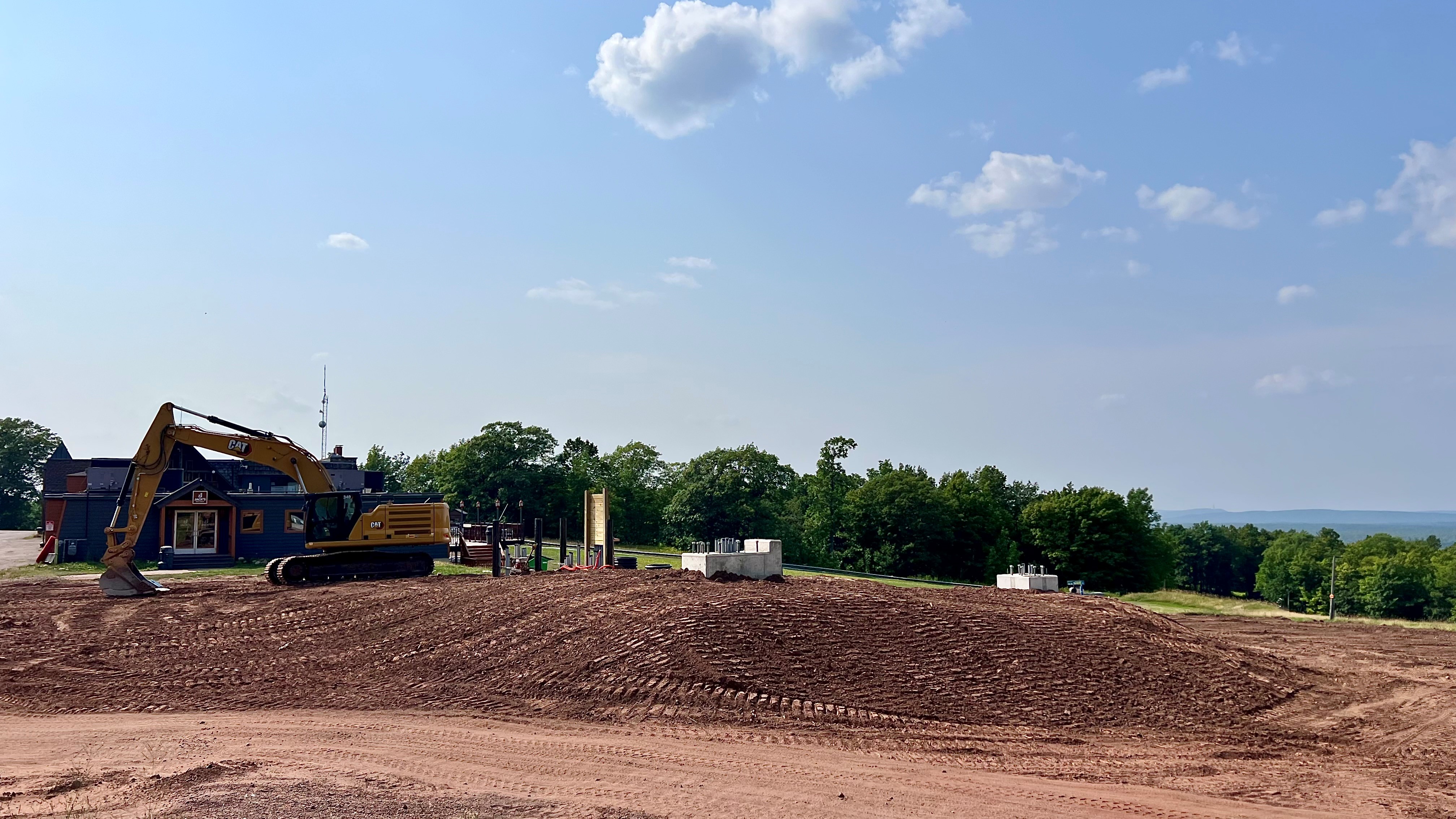
UPDATE: July 25th
After months of work by countless individuals, the time finally came to get the new towers out of the parking lot and stand them up on their foundations. We considered using a conventional crane to lift the towers into place, but the steep terrain would have made it very difficult to move the towers into position and extensive excavation and dozing would have been required to build a crane pad at each tower site. Being that Lutsen is building a lift this summer as well, we choose to partner to split the cost of mobilizing a helicopter from out west to make things a little more efficient for both of us. Saturday, July 22nd, after assisting our friends across the lake with pouring concrete for the new Raptor Express, Brian from Timberline Helicopters pointed his UH 60 Blackhawk across the lake and headed straight for Snowriver. He and his crew touched down here in the main parking lot just after the storm clouds cleared, making for a perfect dust-free landing.
The team arrived at six to make final preparations and conduct a safety meeting with the pilot. You could sense the apprehension as the entire team hung on every word of the pilot's instructions. Having installed 90% of the modern lifts in the American West, Brian was impossibly relaxed and quickly wrapped up his directions with a chipper, "Let's build a lift." At 7:05, the turbine engine slowly spun to life and we all knew the race was on.
Everyone on the team had a predetermined job to do. Brandon and Lee were our yard crew, responsible for connecting the rigging to the helicopter's line. Andrew, Gabe, Michael, and myself were assigned to the ground crew. We were responsible for getting the towers set on the foundations and securely fastened so the climbing crew (Erik, Ryan, John, Josh, Densow, Chip and JR) could get up to the top to catch the cross arms and sheave assemblies. The first order of business for the ground crew was to place "bullets" on top of each of the anchor bolts. The bullets are bright orange, pointed caps that serve to guide the tower onto the bolts while protecting the threads and giving the pilot a clear visual of "home." With the bullets in place, our attention turned to the sky, where we watched for the tower heading our way. As the tower comes into position, the crew signs for the pilot to lower it down to about waist height, where they're able to grab ahold and help guide it into position. With a strong hold on the base of the tower, the pilot slowly lowers the tower down into position until he sees the orange shining through the bolt holes. As soon as he sees it line up, he drops it down into place. Then the ground team springs into action spinning the softball-sized nuts into place. Once the nuts are hand-tight at 12, 3, 6, and 9 o'clock, we signal for the pilot to release his line and he heads back to the yard for the next piece of the puzzle.
As soon as the nuts are tight, my crew runs to the next tower, while the tower team scampers up the ladder to receive the cross arm that's already in the air heading down the hill. Landing the cross arm is similar to the process for the tower tube, but instead of the orange bullets, two long cable "snakes" are used to align the cross arm. The snakes are 15-foot-long cables, threaded through two of the bolt holes on either side. As the pilot brings the cross arm into position, the person on the top feeds them down through the corresponding bolt holes on the tower tube.
Once through the holes, each person on the tower grabs a snake and pulls as hard as they can. The pilot can feel the tugging, signaling him to gently lower the cross arm into position. Once set, the top guy breaks free the bolts zip tied to the cross arm and quickly puts them into place so the heli can head back for its next load. The final step in the process for each tower is to attach the sheave trains. Sheave trains are what we call the row of wheels that will eventually support the cable and chairs. As soon as the climbing crew gets the cross arm bolted down, they crawl up onto the catwalks to wait for the chopper. The brackets that attach the assembly to the cross arms are held open by custom spacers with an integrated set of handlebars. As soon as the handlebars get within reach, the tower crew grabs ahold and slides them onto the square tube on the end of the cross arm. The helicopter gives it a quick pull towards the center of the tower before lowering the rigging down to release it. The process is then repeated on the other side. All in all, it takes less than 30 minutes to fully assemble each tower. Hard to beat that level of efficiency!
UPDATE: July 8th
The team from Ruotsalas has completed pouring concrete and backfilled the foundations for Towers 2-10. This leaves Tower 1 and all four terminal foundations to complete but is still a big milestone as it allows us to revegetate the access roads created to reach tower locations on the side of the hill. The rest of the pours are much more easily accessible via pre-existing and solid roadways, meaning rainy weather is much less of a threat to our forward progress.
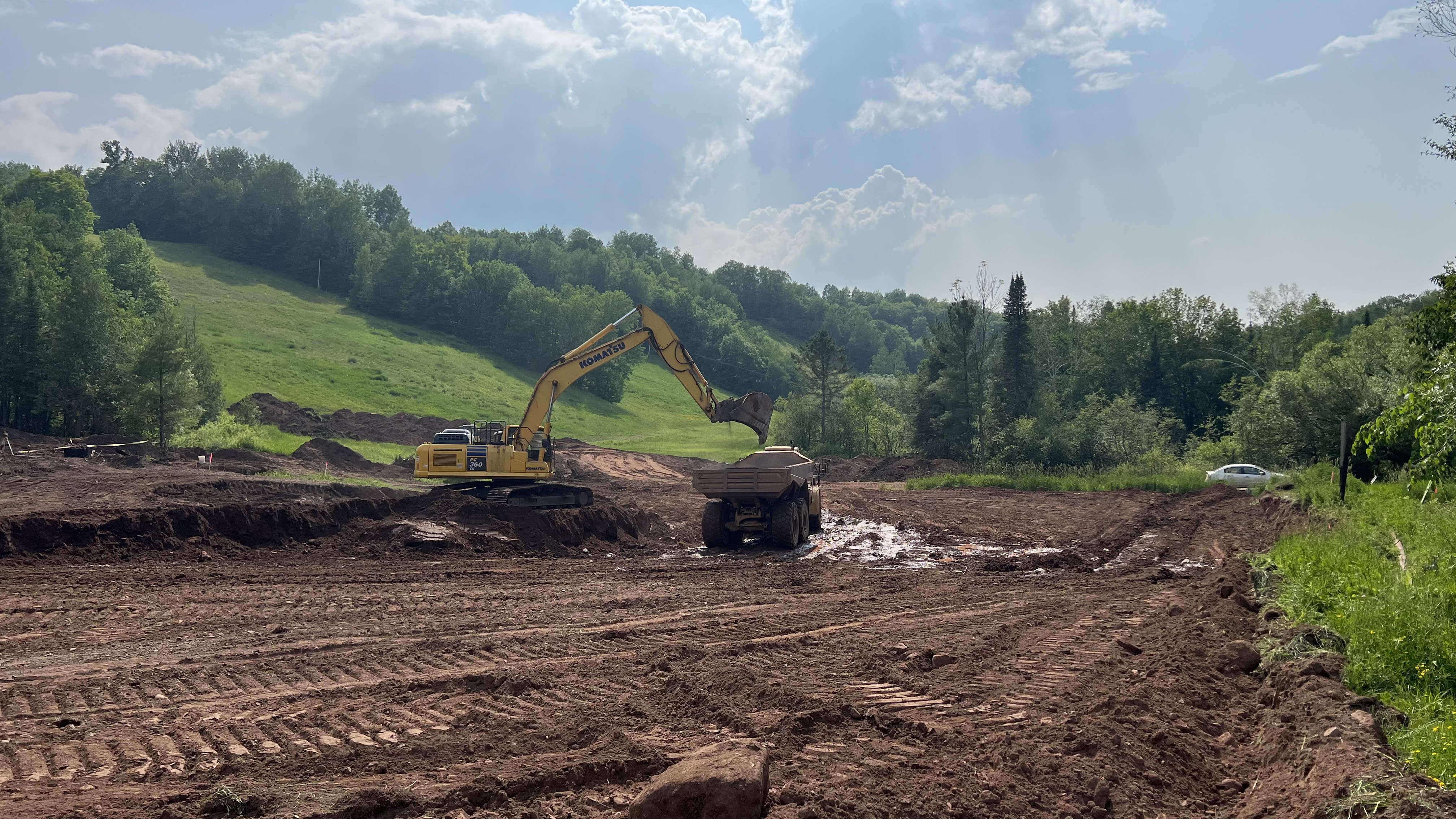
With the Tower foundations substantially completed, the focus shifts to the top and bottom terminal locations. At the bottom, we are undertaking a massive regrading project to improve skier access to the lift from both the east and the west sides. The loading mound of the former triple lift has been completely removed and redistributed at the bottom of Borealis (FKA Leelinaw). This will create a consistent downhill pitch from the foot of the hill all the way to the lift loading area. I'm excited for my first run down Borealis this season without having to push or skate my way uphill to the lift. To the east of the new terminal, up to 10 feet of material has been removed to create a consistent grade from Creekside all the way down to the loading area.
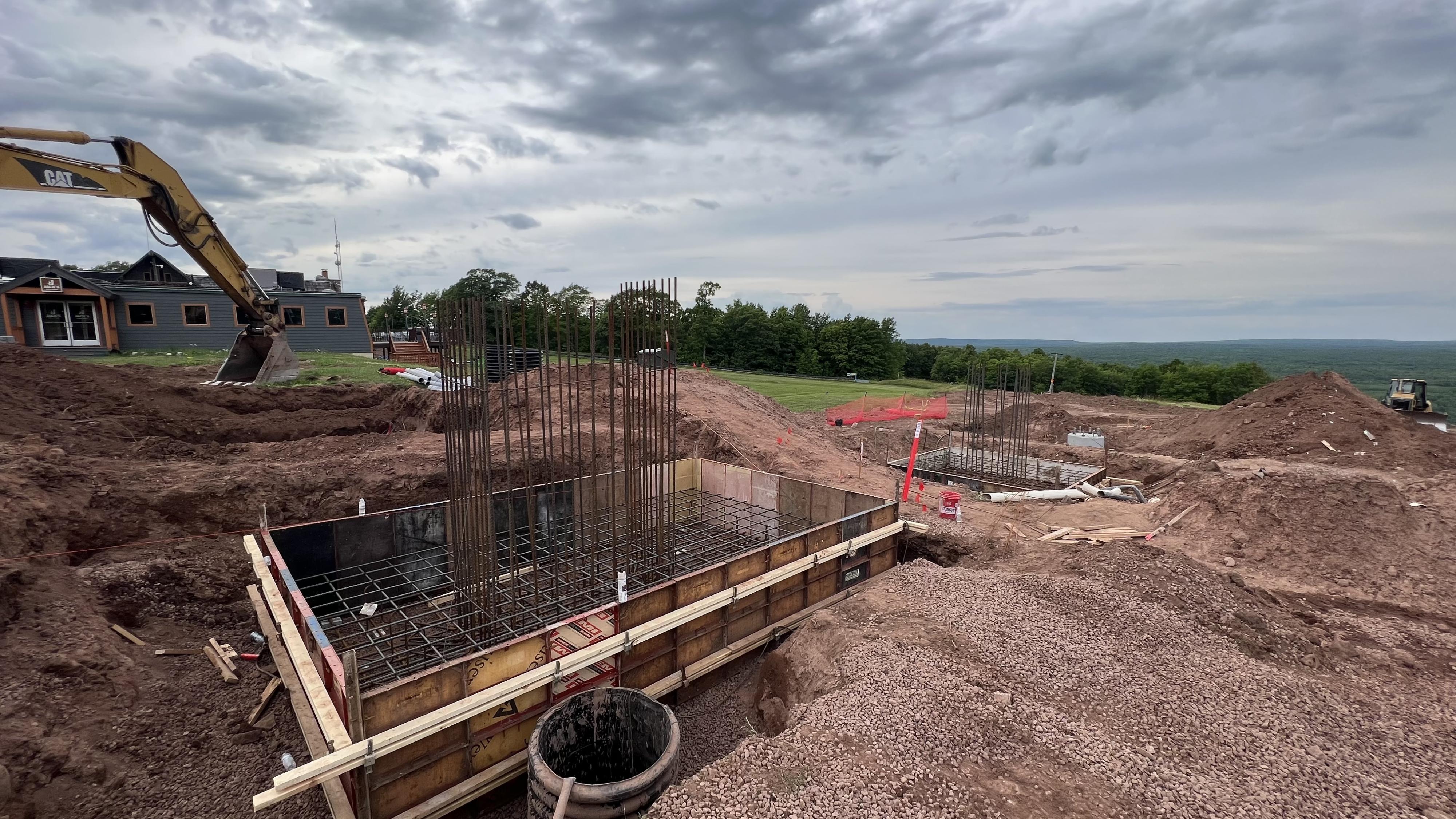
Three months after we were meant to break ground on the drive terminal we are finally in the ground. We ran into a number of surprises earlier this spring when we first had utilities located. Within the 20' x 20' area that the top terminal foundation was meant to go we found the primary electrical service, water main, and greywater discharge lines for the Summit Chalet. All of these utilities needed to be relocated before we could begin excavation. Unfortunately getting the necessary permits in hand to complete this work took longer than expected. I appreciate the work of our partners at Xcel Energy, the Gogebic Range Water Authority, Section 32 Sewer Authority, C2AE, and Ruotsala's Construction in helping us to get this done as quickly as possible.
Despite the delays on this portion of the project, we are still on schedule for an on-time completion as we shifted the tower foundations to the start of the project when those weren't originally scheduled to be started until the 1st of July. Shovels hit the dirt at the top terminal site this past week and thanks to the quick work of the teams, we expect to pour the first round of concrete the second week of July.
UPDATE: JUNE 5TH
After the initial pour is complete and curing has begun, the initial forms are stripped and the work begins to build the cage for the concrete pier. This section contains the anchor bolts that will secure the lift tower to the concrete base. This is a critical portion of the build as each anchor bolt's location needs to be precisely in the right location to align with the pattern specific to each tower. Our project manager from Dopplemayr uses special surveying equipment to verify the correct location of each anchor bolt before the pour is authorized.
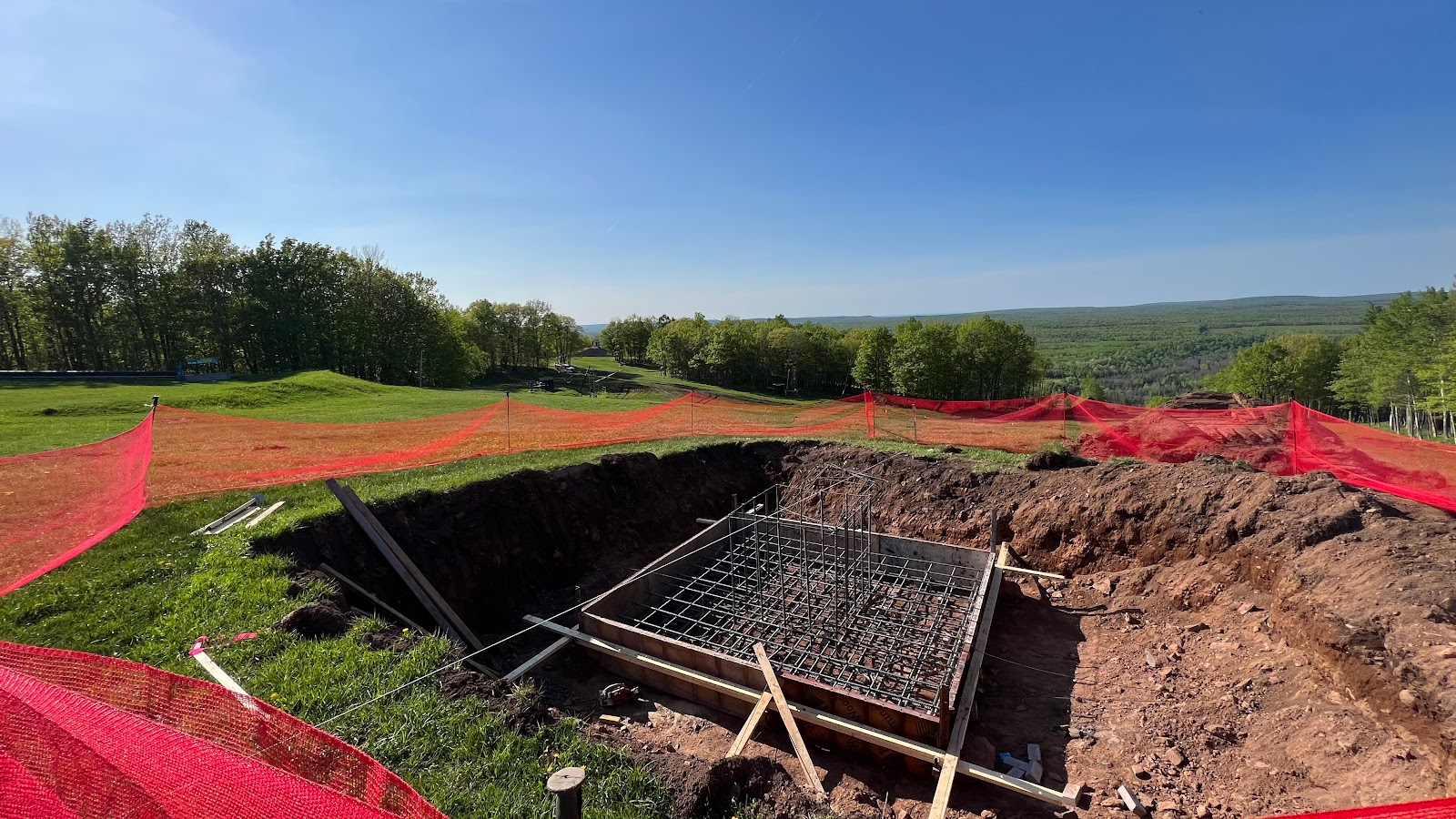
Last week (week of May 29th) the footing bases were poured on 9, 8, and 7 while the forms were prepped on 6, 5, and 4. This week (week of June 5th) the concrete trucks will be back on site to pour the piers for 7-9 and the bases for 4-6. The image below shows the approximate location of each tower along the new lift line. If you look closely you can see the access road that has been carved into the hillside to allow concrete trucks to make their way down to each of the tower sites. Getting all of the tower concrete poured will be a huge milestone for the project and if the weather continues to be in our favor, we may see this wrap-up by the end of June.
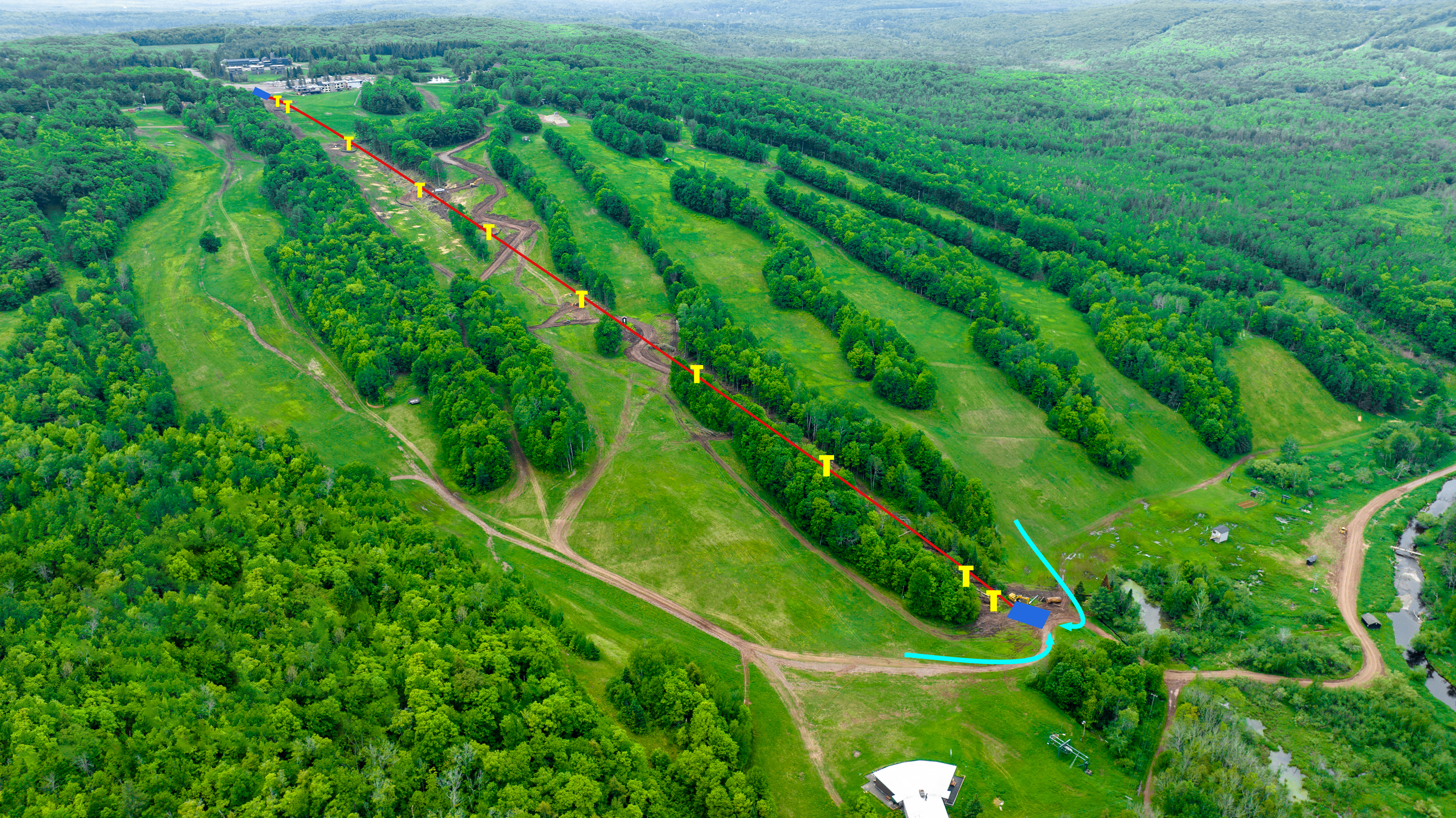
UPDATE: May 16th
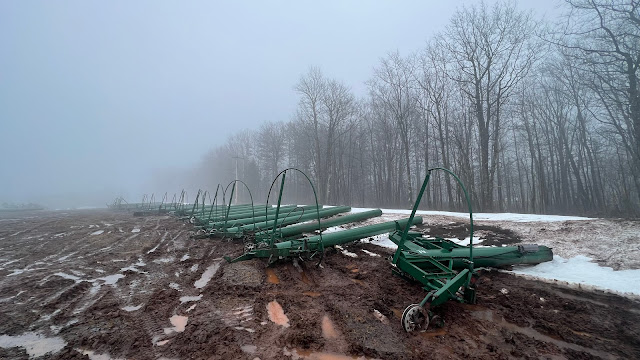
The mountain crew had a monumental task on their hands to dismantle, remove and scrap three chairlifts made up of over 5 miles of steel cable, 65 steel towers, 6 terminal structures, and 3 concrete vaults. Once all the towers had been cut and hauled up to the overflow lot, work began on torching them apart to allow them to be loaded onto trailers for the trip to the scrap yard. To date, we've hauled 160,000 pounds of metal to the scrap yard to be recycled, with more yet to go.
While one crew has been dedicated to removing the old lifts, another has been entirely focused on clearing trees from the upper section of the new lift line between Alpenglow and Superior. Brian and his crew have been busy cutting trees and chipping brush.
UPDATE: APRIL 17TH
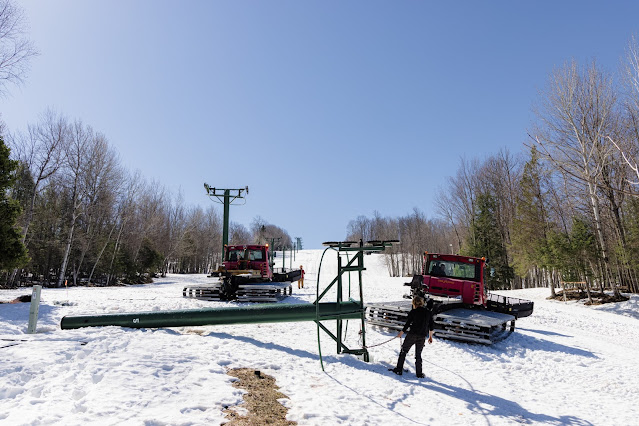
In the few days since we've closed for the season a ton of work has already gone into disassembling and removing the Quad, Triple, and Double to make way for construction to begin on the Voyageur Express Six. First, crews gently lowered the Original Double's haul rope (wire cable that holds the chairs) onto 4x4s. The wood will protect the rope as it is reeled up over the ground keeping it in perfect condition so that it can be used to replace the current haul rope on the Bear Creek Double later this summer.
Spooling up fifteen thousand pounds of cable stretched out over six thousand feet is no small task, so we enlisted the help of JT and his son Jake from Mountain Wire Rope Service. They came all the way from Pennsylvania with their custom-made spooling machine in tow to help us out. Once the spooling machine was set up, the splice was cut right at the marriage, and one end was attached to the large blue spool shown in the photo below. Once the machine got to turning, the team spent the next two days carefully guiding the rope down the hill around the bull wheel at the base and all the way back up and onto the spool.
The project started on a beautiful warm spring Saturday and by the time the tail end of the rope made its way to the reel on Sunday, we were well into a fierce winter storm. I can't thank the crew enough for sticking it out and working through miserable conditions to wrap it up. With 15k pounds of cable on the spool and a worn and frozen crew ready to head home, we needed to pick the spool up out of the machine and stage it in the parking lot. For this, we looked to our friends at Ruotsala Concrete of Ironwood who have already dropped off their biggest excavator to help dig out the foundations for the new lift. My thanks to Colin for coming out on a Sunday in the freezing rain and snow to help us out!
With haul ropes out of the way, the team began the removal of the 75 towers that will come down this summer to make way for wide-open skiing and riding next winter. Our team mounted a set of torches on the back of a snowcat and made their way from tower to tower, cutting all but a small portion of the tower before connecting a cable to the top and pulling it over with another snowcat. Once on the ground, each tower was dragged over the snow to the mountaintop parking lot where it will be cut up and sent off for recycling.
Removing all of these towers from the slopes is going to have a huge impact on the way the mountain skis next winter. Borealis feels like a huge Western cruiser without its towers and the Voyageurs funnel doesn't feel so quite so narrow. Going from 75 towers down to just 10 hidden on trail edge is going to create plenty of opportunity for wide-open cruising on the main face. Check out the before and after photos below!